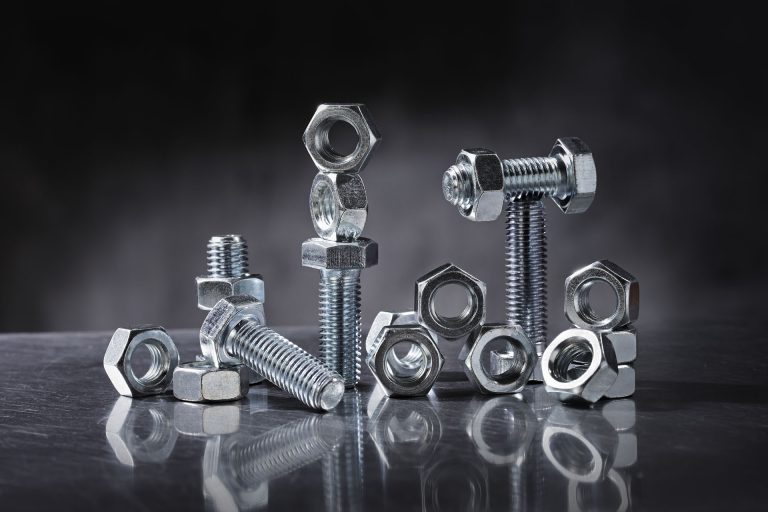
If you want your fasteners, bolts and screws to last longer, you can do several things to prevent thread galling. Keeping them clean, using lubricants and minimizing installation speeds all help reduce the likelihood of galling occurring.
Adding an anti-seize compound to the mating materials is one of the most effective ways to reduce galling. There are a variety of these lubricants available; consult with a representative to find an anti-seize that will be safe for your application.
Friction
During tightening, friction causes heat to build up between the mating threads. This heat is generated by the metal-to-metal contact and shears through the protective oxide layer, causing the two materials to fuse together in a process called cold welding. This shearing of the protective coating is what initiates galling and can eventually cause the mating parts to seize.
The occurrence of galling can be prevented by using premium quality fasteners, following torque specifications and lubricating the threads before installation. Also, slowing the installation RPM speed can decrease the chance of galling, since faster tightening creates higher temperatures on the thread flanks before they can dissipate.
Axial misalignment between clamped components, extraneous loads between clamped components introduced during assembly or handling, and incorrect threading can also increase the risk of galling. Additionally, nicking or denting fasteners before use can significantly increase the risk of galling. It’s recommended to use clean fasteners and inspect them for defects before installation.
Heat
The frictional process that results in thread galling is accompanied by the generation of heat. Fortunately, heat can also be a factor that prevents galling. Slowing down the installation rpm speed will frequently reduce or solve the problem of galling because it allows more time for heat to dissipate between the fasteners.
Stainless steel hardware produces its own protective oxide film to prevent corrosion and is prone to galling when the coating is rubbed off during tightening or installation. The resulting direct metal-to-metal contact generates friction that clogs, shears and locks the threads, which then fuse together into a condition known as “galling.”
Pre-applied lubricants can greatly reduce the chances of galling by providing a protective layer between the materials that prevents them from rubbing directly against each other. Dry film lubricants containing molybdenum disulfide, graphite, mica or talc are particularly effective. PTFE (Teflon) and other fluoropolymer coatings are also good choices, but must be used with care in environments where corrosive materials are present.
Debris
If you’ve spent any time in mechanical system assembly, operation or maintenance, you know that even a small amount of galling can disrupt an entire project and cost huge money. A severe case of galling can cause the threads of a bolt to unintentionally fuse together with the threads of a nut or tapped hole. This is sometimes called cold welding and results in the parts becoming so seized that they can’t be removed without cutting or splitting them.
The good news is that almost all cases of galling are preventable. Lubrication can be a big help, and premium fasteners are often designed to reduce galling. Even if they can’t be lubricated, a little care like using clean, undamaged bolts and carefully tightening them (not over-tightening) will greatly reduce the chance of galling. A wire brush cleaning before reassembly is a great idea too. A quality dry lubricant like Neolube can also greatly reduce galling risk.
Materials
When galling happens, material from one surface adheres to the mating surface and creates a lump that shears during further fastening. This clogging, shearing and locking of surfaces creates more friction as the two materials try to slide over each other. Eventually, the materials will fuse together and become stuck, or even “seize” completely, making them impossible to remove.
Galling is a common problem that occurs in stainless steel and other soft metals like aluminum and titanium. These materials generate their own protective oxide films to prevent corrosion but these can be rubbed off during installation and tightening pressures. The resulting direct metal-to-metal contact creates heat that can cause the materials to fuse and seize.
The most effective way to reduce the chance of galling is to keep all thread surfaces clean and to use a good lubricant. Lubricants with high levels of molybdenum disulfide, graphite, mica and talc are effective at reducing friction. PTFE (Polytetrafluoroethylene) coatings also help to eliminate galling in some applications.